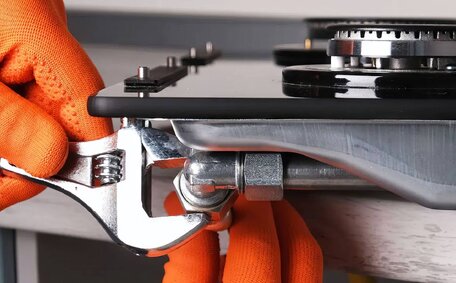
The role of gas fitting in kitchen renovations
When renovating your kitchen, it’s important to engage a licensed gas fitter to safely install, replace or alter any gas appliances and pipes. This ensures
Read MoreAs buildings grow taller to accommodate urban expansion, maintaining plumbing systems becomes increasingly complex. Traditional pipe repair methods often require breaking concrete floors and walls to access pipes, resulting in major disruptions. Does pipe relining offer a revolutionary trenchless solution? Yes, it restores pipes with advanced pipe repair technology from the inside via small access points with minimal disruption.
The pipe relining process involves inserting an epoxy resin-soaked liner into damaged pipes through an open end. As it hardens, the liner adheres to your existing old one, creating a smooth new pipe within the broken one.
Once in position, technicians use hot water, steam, or UV light to cure the resin. Once in position, technicians use hot water, steam, or UV light to cure the resin.
For multi-story buildings, the pipe relining work was very effective at avoiding major concrete demolition. Accessing vertical stacks of plumbing, housing sewer pipe systems, can require jackhammering through multiple floors, resulting in significant expense and tenant disruption. Pipe relining inserts new pipes from a single point, drastically reducing restoration time, cost and impact.
As Sydney’s population grows, multi-story apartment blocks and commercial towers are increasingly common. Learn how pipe relining enables non-destructive plumbing maintenance in these complex structures. Read on to know about pipe relining and how it works for optimal reliability.
High-rise buildings near your home present distinct plumbing challenges, with pipe relining being the solution that addresses the vertical complexities of these systems. Occupants often encounter issues, specifically broken pipe dilemmas:
As high-rises age, issues become prevalent and they would often find that problems with pipes intensify. Yet they would find that carrying out repairs is complex due to layered concrete construction between floors. Breaking through slabs to access plumbing can cost thousands per affected area.
Trenchless pipe repair, exemplified by pipe relining, provides a minimally invasive solution by using trenchless technology. Using a specialised CCTV drain camera, technicians first skate through the pipes to assess damage via existing openings. This process essentially fabricates new pipes without leaching materials into soil or necessitating any jackhammering.
There was careful preparation as liner materials were then saturated with epoxy resin and fed through the same access points. In any plumbing repair, technicians use hot water, steam or UV light to cure the resin, ensuring it bonds securely to pipe walls.
For high-rises, pipe relining can restore damaged pipe functionality and boost longevity at a fraction of the invasiveness, time and cost of the traditional method. By accessing pipes from single entry points, extensively layered concrete teardown is avoided. This makes relining an extremely viable option for multi-story buildings everywhere.
Understanding how pipe relining is carried out in tall structures necessitates knowledge of the specialised equipment and careful planning regarding access points. Key equipment used includes section pipe repair tools:
Gaining entry to vertical plumbing stacks often relies on openings like vent pipes on upper floors. With modern methods, plumbers can use CCTV technology to navigate the repair sites without the extensive use of scaffolding or elevated platforms. The non-destructive nature of relining inserts avoids having to break concrete floors and walls between pipe joints.
Navigating the maze of plumbing in large structures requires expertise. By using advanced technology, technicians can pinpoint the damaged section to repair your pipes and determine the best access strategy with minimal intrusion. Effective techniques ensure all custom-fitted liners reach the relined section for restoration with precision mapping and measurement.
With specialised tools and strategic access planning, pipe relining enables non-destructive refurbishment of essential plumbing, regardless of building scale and complexity. Leaving concrete intact makes it an extremely versatile and low-impact approach for structures both tall and small.
Executing the pipe relining procedure can also be seen as a precise, multi-step process to fashion seamless results. The key stages are:
The new seamless pipe within pipe restores functionality for decades, without any major destruction to building walls and floors. Regular maintenance maximises longevity of pipe relining projects in multi-story buildings.
When it comes to restoring a worn-out plumbing system, pipe relining offers a fast, affordable and low impact solution compared to pipe replacement.
By renovating pipes from the inside, it sidesteps the excessive damage and disruption, rather than breaking into concrete slabs. Advanced repair materials like epoxy resin liners can now rival or exceed the lifespan of new copper pipes too.
Unless whole-system revamps are essential, pipe relining enables non-destructive restoration of any leaks, cracks or blockages in multi-story buildings. Strategic access planning facilitates the procedure for relining pipes through existing openings, even in vertical arrays. This unique benefit for high-rises makes it an extremely versatile maintenance option.
Trenchless pipe relining offers numerous advantages over traditional open-trench pipe replacement methods:
By renovating pipes from the inside-out, pipe relining technology enables non-destructive restoration of plumbing systems with multiple economic and ecological benefits. The technology upholds both tenant convenience and environmental stewardship, making it the sustainable choice for modern buildings everywhere.
Implementing pipe relining in sewer pipes of a multi-story building requires careful evaluation of key factors beforehand, including:
Proactive building managers invest in regular pipe inspections by qualified providers of plumbing services. Thorough assessments outline relining plans that preclude further damage while balancing costs, tenant convenience, and long-term functionality. Strategic access planning also streamlines installation with minimal interference.
Pipe relining remains the least invasive, most affordable trenchless solution for restoring ageing plumbing in inhabited multi-story structures. When damage is caught early, it can significantly extend the lifespan of entire systems too. By partnering with expert technicians, building managers ensure that your plumbing receives cutting-edge care through internal pipe renewal techniques.
To guarantee effective pipe relining outcomes in multi-story buildings, partnering with qualified plumbers is key. When selecting a professional relining company like Cecil Hills Plumbing, check for these signs of expertise:
Reputable plumbers follow best practise installation methods for lasting results. This includes:
Allowing experts to handle your pipe relining ensures non-invasive, long-lasting restoration. Regular drain maintenance then maximises the lifespan of your building’s renewed plumbing.
As buildings grow taller and more complex, maintaining structural integrity and essential systems becomes increasingly vital. Pipe relining provides building owners with an innovative pipe repair solution that upholds plumbing functionality and minimises disruption for occupants.
Unlike traditional pipe replacement methods requiring breaking concrete floors and walls, relining is a trenchless technology restoring pipes from the inside out. Tiny cameras first assess damage through existing openings. Custom-fitted epoxy resin liners are then fed through the same access points to coat damaged areas, essentially creating a pipe inside seamlessly within old ones.
Pipe relining can restore leak-proof performance for 50+ years thanks to durable resins. Strategic access planning from single entry points also eliminates the need for destructive access through layered concrete. With residents experiencing negligible inconvenience, it’s an extremely viable and versatile maintenance option, even divided into units.
As urban centres like Cecil Hills in Sydney’s st east continue growing upwards, pipe relining enables smart building managers to maintain and strengthen ageing plumbing infrastructure. Protecting investments in multi-story properties while upholding tenant convenience makes trenchless methods a clear choice for sustainable buildings now and in the future.
To learn more about revolutionising your property’s plumbing with pipe relining, call Cecil Hills Plumbing today on 1300 349 338 or email jobs@cecilhillsplumbingservices.com.au to book your consultation. Our team brings decades of experience delivering proven pipe renewal solutions in complexes large and small.
When renovating your kitchen, it’s important to engage a licensed gas fitter to safely install, replace or alter any gas appliances and pipes. This ensures
Read MoreGas line repairs require a licensed plumber to locate any leaks, fix damaged pipes and fittings, and properly seal everything to prevent future issues. Contact our emergency plumbers for safe and proper gas line repairs.
Read MoreDuring emergency plumbing situations, crucial safety precautions include turning off the main water supply to prevent flooding, wearing protective gear to avoid injuries, clearing standing water to minimize damage, and calling a licensed professional plumber for assistance.
Read MoreCecil Hills, 2171 NSW
We will call back as soon as possible.